


Mantenimiento predictivo: Claves para minimizar averías y mejorar el rendimiento
En la constante búsqueda por la optimización de procesos y la minimización de costes, las empresas de hoy en día se encuentran en una encrucijada donde la tecnología y la innovación son sus principales aliados.
Una de las áreas que ha experimentado una transformación significativa es el mantenimiento industrial, especialmente con la llegada de la Industria 4.0. En este artículo, exploraremos cómo el mantenimiento predictivo, basado la condición, se ha convertido en una herramienta esencial para reducir los tiempos de inactividad, garantizar la eficiencia y supervisar equipos de forma remota.
Mantenimiento basado en la condición: el origen del mantenimiento predictivo
Para comprender la importancia del mantenimiento predictivo, es fundamental remontarse a sus raíces en el mantenimiento basado en la condición (CBM). El CBM es una estrategia que se centra en el estado actual de los equipos y maquinaria en lugar de realizar mantenimientos de rutina programados. En otras palabras, se basa en el monitoreo constante de la salud de los activos industriales (maquinaria) para determinar cuándo es necesario intervenir.
La revolución en el CBM ha llegado con las tecnologías avanzadas, siendo los sensores de última generación la columna vertebral de esta estrategia. Estos dispositivos pueden medir una amplia variedad de parámetros, como la temperatura, la vibración, la presión y la humedad, proporcionando datos en tiempo real sobre el estado de las máquinas. Estos datos se transmiten a sistemas de análisis que utilizan algoritmos avanzados para evaluar la salud de los activos y predecir posibles fallos.
El CBM sienta las bases del mantenimiento predictivo al centrarse en la prevención de problemas antes de que ocurran, demostrando ser altamente efectivo en la reducción de costes y la maximización de la vida útil de los equipos. Sin embargo, el mantenimiento predictivo va más allá al incorporar herramientas digitales y análisis de datos más sofisticados.
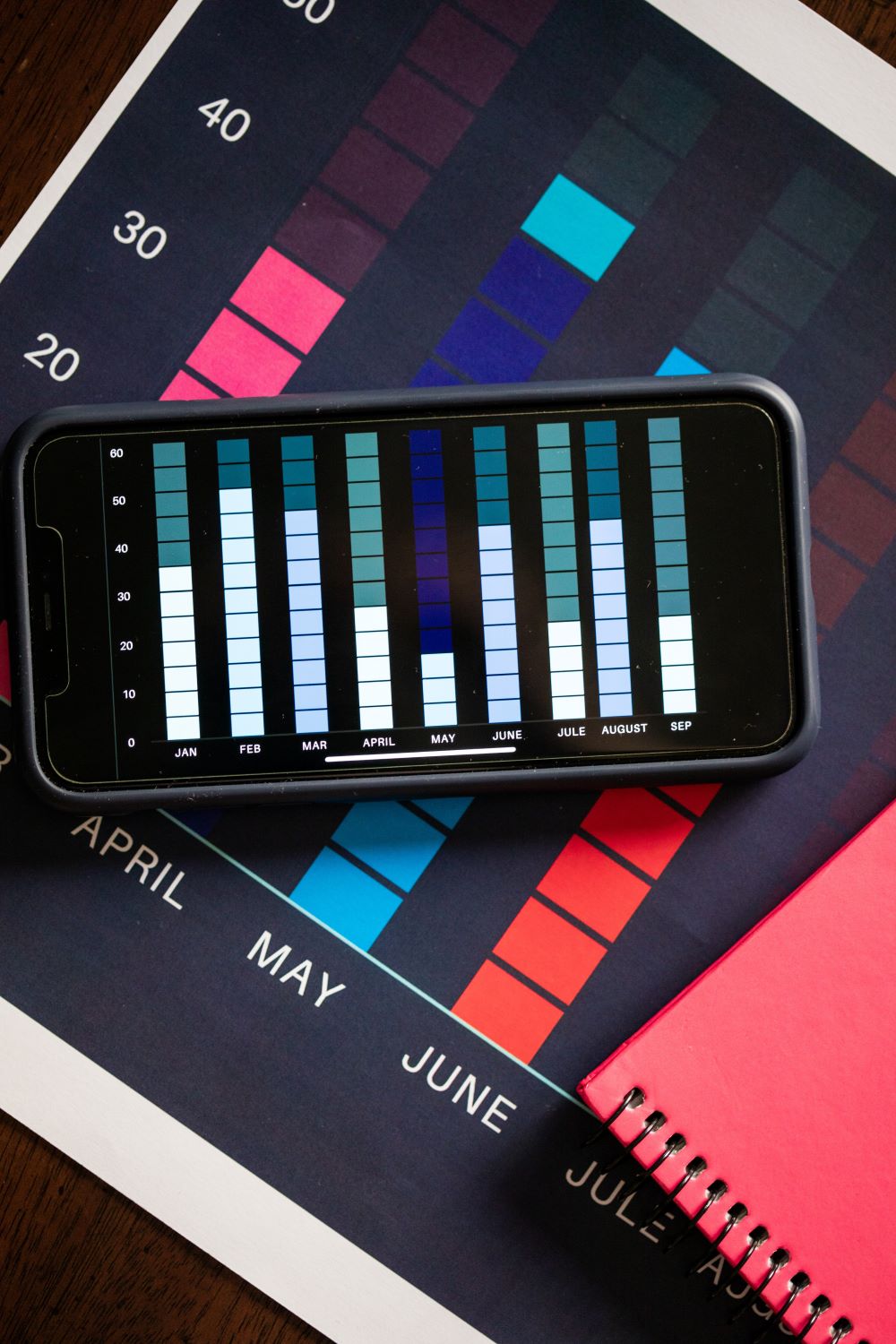
El papel de las personas: colaboración activa y capacitación
Aunque la tecnología es esencial en la implementación del mantenimiento predictivo, no se puede pasar por alto el papel tan importante que desempeñan las personas en este proceso. El éxito de esta tecnología requiere colaboración activa y la capacitación adecuada de los empleados.
Para que el mantenimiento predictivo funcione de manera efectiva, es fundamental contar con personal capacitado para interpretar los datos recopilados y tomar decisiones basadas en ellos. Esto implica la formación de técnicos y personal de mantenimiento en la interpretación de datos y el uso de las herramientas de análisis disponibles. Además, se necesita una colaboración estrecha entre los equipos de mantenimiento y producción para coordinar las intervenciones de manera eficiente y minimizar los tiempos de inactividad.
La adopción tecnológica también implica inversión en infraestructura y sistemas que respalden la recopilación y el análisis de datos. Esto incluye la instalación de sensores en la maquinaria, la configuración de sistemas de monitoreo en tiempo real y la implementación de software de análisis de datos avanzados. Es crucial que las empresas estén dispuestas a comprometerse con estos recursos para aprovechar al máximo los beneficios del mantenimiento predictivo.
La cultura organizacional juega un papel crucial en la adopción exitosa de la tecnología de mantenimiento predictivo. Las empresas deben fomentar una cultura de innovación y mejora continua, donde la adopción de nuevas tecnologías se vea como una inversión en la eficiencia y la competitividad a largo plazo.
Ventajas del mantenimiento predictivo
Ahora que hemos explorado el origen y la importancia de la tecnología de mantenimiento predictivo, es el momento de analizar las ventajas que ofrece a las empresas que optan por implementarla en sus operaciones.
Minimización de los tiempos de inactividad: Una de las ventajas más evidentes del mantenimiento predictivo es su capacidad para prevenir fallos no planificados. Al monitorear constantemente los equipos, las empresas pueden identificar problemas potenciales antes de que se conviertan en averías costosas. La anticipación y resolución proactiva de problemas contribuyen a una planificación más eficiente del mantenimiento, reduciendo los tiempos de inactividad y evitando pérdidas de producción.
Aumento de la eficiencia operativa: Al evitar paradas no programadas y realizar mantenimiento de manera predictiva, las empresas pueden aumentar la eficiencia de sus operaciones. Los equipos funcionan de manera más confiable y consistente, lo que se traduce en una producción más constante y un mejor uso de los recursos.
Reducción de costes de mantenimiento: El mantenimiento predictivo permite programar intervenciones de manera proactiva en función de las necesidades reales de los equipos. Esto evita el desperdicio de recursos en mantenimiento preventivo excesivo y reduce los costes asociados con la reparación de averías graves.
Mayor vida útil de los activos: Al detectar y abordar problemas en etapas tempranas, el mantenimiento predictivo contribuye a prolongar la vida útil de los activos industriales. Esto significa que las empresas pueden aprovechar al máximo su inversión en maquinaria y equipos.
Control remoto de la maquinaria: Con la tecnología adecuada, el mantenimiento predictivo permite supervisar y controlar la maquinaria de manera remota. Esto es especialmente valioso en entornos industriales, donde la ubicación de los equipos puede ser remota o de difícil acceso. Los técnicos pueden realizar diagnósticos y ajustes sin necesidad de desplazarse físicamente.
Mejora en la seguridad: Al prevenir fallos inesperados, el mantenimiento predictivo contribuye a mejorar la seguridad en el lugar de trabajo. Reduce el riesgo de accidentes relacionados con el mal funcionamiento de la maquinaria y protege la integridad de los empleados.
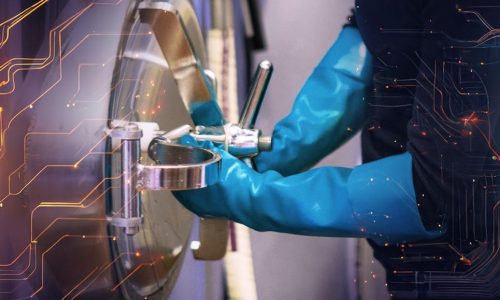